How Are Forged Ring Forgings Manufactured?
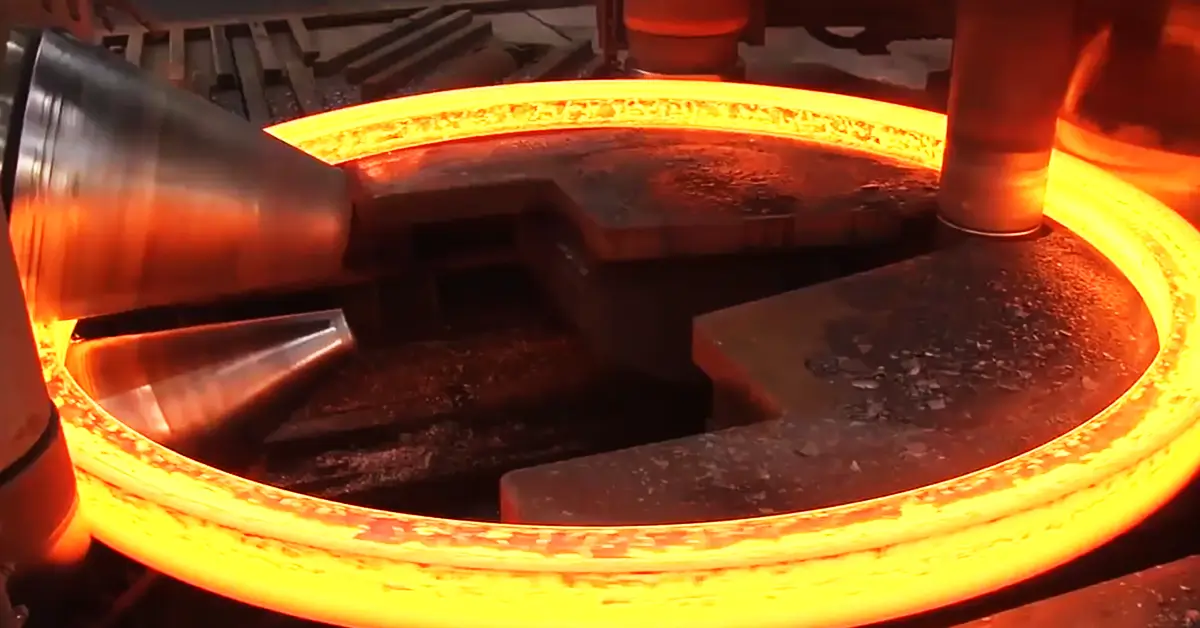
A forged ring is an indispensable component in many critical pieces of equipment in modern industrial manufacturing. It is widely used in various fields due to its superior performance and reliable quality. At Songjie, we provide high-quality forged ring forgings through optimized manufacturing processes. So, how exactly are ring forgings made? What technical details lie behind this process? This article will take you through how Songjie creates high-precision, high-performance forged rings.
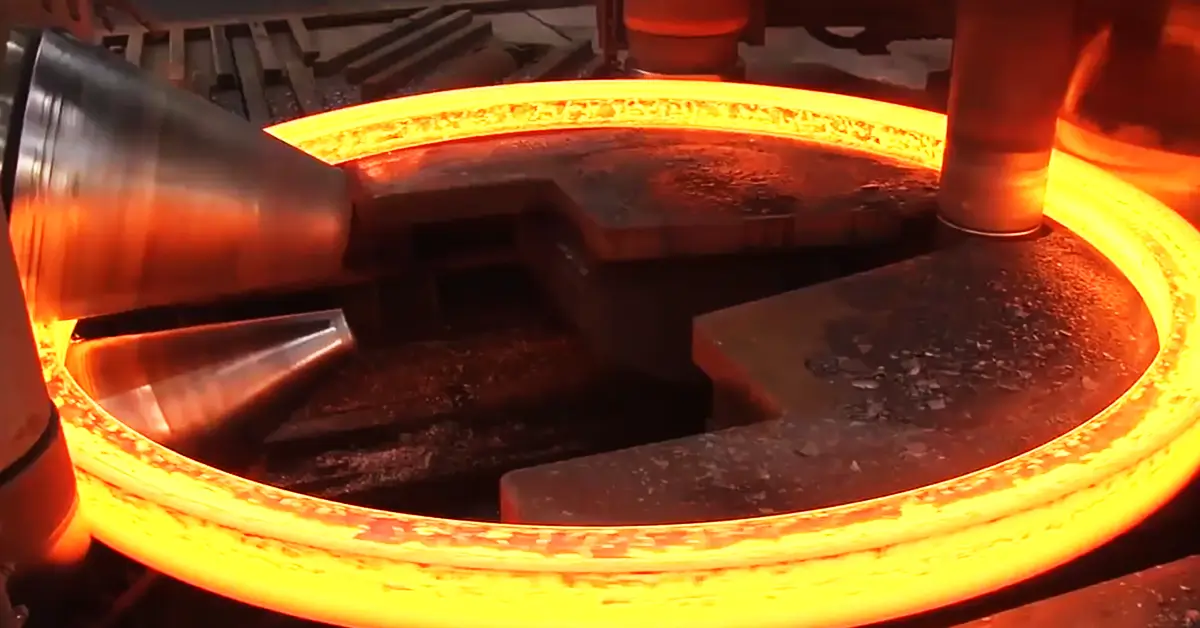
I. Rigorous Screening of Raw Materials
The quality and performance of forged ring forgings are closely related to the selection of materials. At Songjie, the commonly provided forging materials include alloy steel, stainless steel, aluminum alloy, nickel-based alloy and other materials. These steels need to meet strict manufacturing standard requirements in terms of key performance indicators such as hardness, toughness, strength and purity. We will conduct a comprehensive inspection of each batch of raw materials. Any slight deviation can’t escape our “sharp eyes”. Only the raw materials that have passed strict screening layer by layer are eligible to enter the subsequent manufacturing process.
Actual Case: For the forged ring forgings applied in aero engines, the raw materials must have extremely high high-temperature strength and oxidation resistance. Therefore, customers usually require the use of high-nickel alloy steel to ensure reliable operation under extreme working conditions.
II. Forging Process Flow
1. Heating
Before forging, the selected raw materials are first heated. Generally, they are heated to a range of 850°C to 1200°C (the heating temperatures vary for different raw materials) to improve their plasticity, reduce the deformation resistance, avoid the occurrence of cracks, and ensure that they reach the optimal forging state. At Songjie, every parameter during the heating process has been carefully calculated and repeatedly verified, just like a precise scientific experiment.
2. Forging Process
The heated material is subjected to pressure through multiple forging hammers or hydraulic presses, causing the material to undergo plastic deformation to form the required shape and size. During this process, the temperature and pressure need to be well controlled to ensure uniform deformation of the material.
Subsequently, it enters the ring rolling process. The preliminarily formed ring blank is placed on the ring rolling machine. Through the rotation and feeding of the rolls, the ring blank is further rolled. The inner diameter is gradually expanded, and the outer diameter and wall thickness are controlled to make the wall thickness uniform and the dimensional accuracy meet the design requirements, finally forming the required ring structure. Throughout the forging process, the advanced automatic control system monitors various parameters in real time, strictly controlling the inner and outer diameters, height, and wall thickness of the ring. Once an abnormality occurs, adjustments are immediately made to ensure the stability and efficiency of the forging process. The ring rolling process can not only improve the dimensional accuracy of the ring forgings but also further optimize their internal structure, enhancing the mechanical properties and fatigue life of the products.
3.Cooling
After the forging is completed, the forged ring forgings need to be cooled slowly to avoid internal stress and cracks caused by rapid cooling, and to increase the hardness of the materials.
III. Heat Treatment Process
After cooling, to further enhance the performance of the ring forgings and meet customer requirements, a heat treatment process is necessary. This process can refine the microstructure of the material, eliminate residual stresses within the forging, and improve its mechanical properties and overall quality, thereby achieving optimal comprehensive performance. It is akin to the final adjustments made by performers before taking their bows at the end of a show, all to leave the audience with the most perfect impression.
IV. Mechanical Machining and Surface Treatment
In addition, some customers require mechanical machining and surface treatment processes, such as turning, grinding, shot peening, and polishing. These processes can further enhance the surface quality of the forged ring, reduce stress concentration, and extend its service life, thus achieving the required dimensions and surface finish as specified in the design.
V. Final Product Inspection
Forged ring forgings require rigorous and comprehensive final product inspection. Common inspection methods include:
Visual Inspection: Checking for any obvious surface defects.
- Dimensional Measurement: Ensuring that the product dimensions meet design requirements.
- Mechanical Property Testing: Verifying mechanical properties through tensile testing, impact testing, and other means.
- Non-Destructive Testing (NDT): Methods such as ultrasonic testing, magnetic particle inspection, and radiographic testing are used to check for internal defects in the forged ring. This ensures that each forging has uniform internal structure and is free from defects, guaranteeing its safety and reliability during use.
Quality inspection accompanies every stage of the manufacturing process for forged ring forgings. Only by passing strict quality checks can the forgings be delivered for use, ensuring their reliability and safety under extreme operating conditions.
Conclusion
In summary, at Songjie, we produce high-quality forged ring forgings through the above series of processes. The manufacturing process is an interlocking and continuously refined sequence, where each step embodies the wisdom and hard work of our professional team and requires strict control. It is precisely this relentless pursuit of perfection in our processes that makes our forged ring a key force in the industrial sector, enabling us to stand out in the fierce market competition.